If you place an order on Amazon, it can take less than a day to arrive at your doorstep.
But how exactly does that happen?
The Richmond News went behind the scenes of a parcel’s journey - from when an order is placed, to being processed at the Amazon YXX2 Fulfillment Centre in the southeast corner of Richmond, to getting loaded into the Amazon van.
Vendors’ items get stored here, picked, packaged and labeled – the whole process only takes a couple of hours - before they are sent to the assorting centre to be shipped to you, the customer.
During this Prime Day week, 700,000 items are expected to be processed in this very centre in Richmond, which has around 1,000 full-time and part-time employees, according to the company.
An Amazon parcel’s journey, from app to address
In the 400,000 sq. ft. facility, around one third of the space is a “no people zone” full of yellow shelves that are moving around on a four-wheel robot – that is the Amazon inventory and it has another name, the robotic floor.
“This is the brain of the operation,” said Mike Falco, operation manager of the centre.
A parcel’s journey with Amazon starts before a shopper even places an order on their app or website.
Vendors send their products to the centre, where workers scan the items and put them into different cubes on the yellow shelves.
To maximize efficiency, workers put the products from various vendors in random cubes but they don’t need to worry about finding them later, because a camera above the worker will capture workers’ moves to know which item goes to which cube and shelf, and input the information into the computer.
“Once it’s all in those [shelves] on our floor, it’s now available to you on amazon.ca, and you can order it,” said Falco.
When an order is placed, the system will recognize the item in the shelves, moving the shelves to the worker interacting with the robotic floor, who will then pick the item up and send it to the packaging team.
The labeling process is also highly automated. Items get put on a conveyor belt and the system scans barcode on them first to recognize what they are, and then generate a label automatically for each before stamping the label onto the item.
“The system is designed to get you your product as quickly as possible,” said Falco.
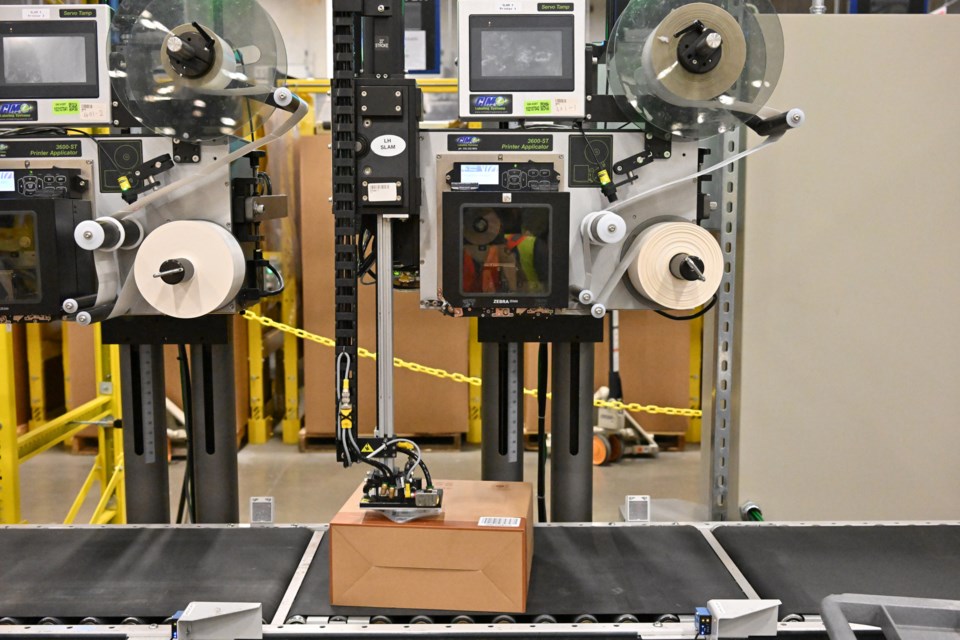
He added that, to minimize mistakes, the system will also weigh the item on the conveyor belt to make sure the weight matches what’s in the system.
There are around five million items at the centre with a nine-week turnover time, according to the company.
Reducing package waste
With the boom of delivery service, packaging waste has also increased. Kishan Rathi, general manager of the Richmond fulfillment centre, said waste reduction has been a priority for the company and is reflected in how things are done in the centre.
“We’ve optimized the packing process to ensure that items that are smaller, are packaged in [fully recyclable] envelopes, to make sure that it’s as efficient and safe for the environment as possible,” said Rathi.
If multiple orders are placed by a shopper, the machine will find all the items in the shelves and bring them to one “picker” who can have the items packaged together.
“That’s how we make sure that we don’t send you seven different packages for seven items,” said Rathi.
“Sometimes all those items are not in this building so we get the items from other building to us first, and then we pick them from the shelf and pack them together.”
The company has also expanded its Shipping In Own Container program through which vendors’ products are shipped without added Amazon packaging, he added.
Amazon has 18 fulfillment centres in Canada and four in B.C.